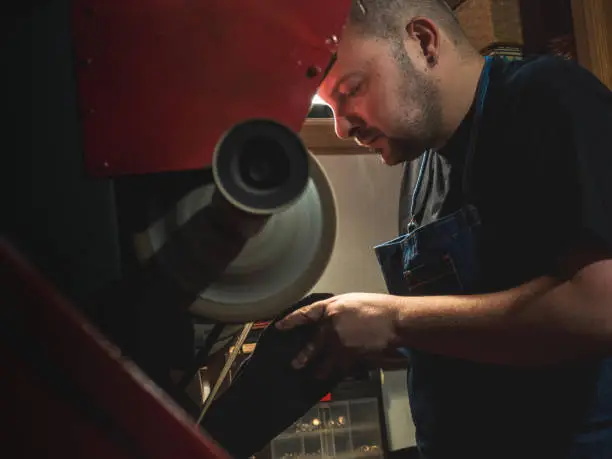
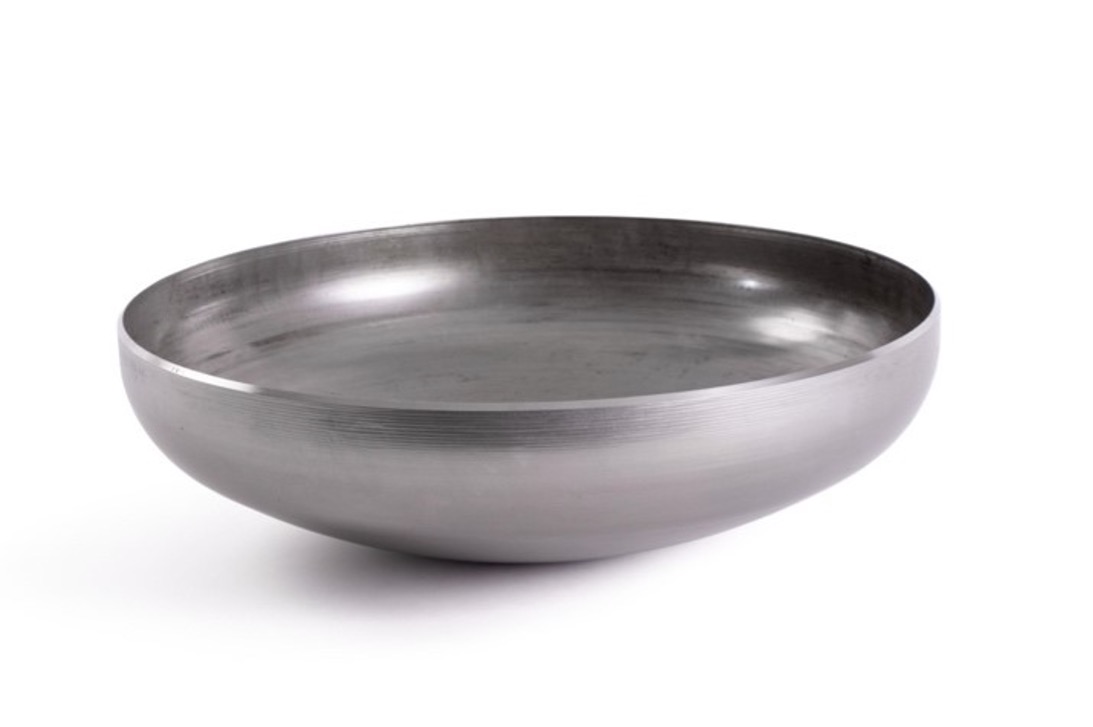
Uses and challenges of flanging dished ends
Dished ends are among the most commonly produced metal spun parts. This is because semi-spherical shapes can easily be produced by the metal spinning process. The addition of the flanged lip on dished ends is often essential, as it allows the part to fit within larger products. If your project requires flanged dished ends, it’s important to be aware of the challenges and potential disruption this process can cause. In this post you’ll find all the information you need to plan accurate project lead times.
What is a dished end?
A dished end is a spun metal part that typically comes in a hemispherical, torispherical, or ellipsoidal shape. Although flat head dished ends (flat flanged ends) can be made when required. Dished ends are rarely a standalone product, instead being produced for the purpose of sealing storage tanks and pressure vessels. This involves multiple metal forming processes, including spinning, flanging, fabrication, and any finishing that’s required. Due to the range of applications dished ends have, they can be used to great effect by businesses in many different industries.
Dished end uses
- Food processing and chemical plants.
- Water tanks.
- Cryogenics facilities.
- Fuel refineries.
- Transportation tankers.
- Air movement systems.
- Renewable energy
- Waste storage.
- Nuclear power.
Challenges in the flanging process explained
The overall shape of dished ends is first formed through metal spinning. Different diameter tooling can be employed to produce dished ends of varying widths and depths. Generally speaking, the larger the dished end the more challenging it is to flange. This is because the more passes that are done on the metal, the more likely it is to develop defects along with work hardening during the metal spinning process.
Flanging dished ends is done with a specialised cold rolling machine. In most cases, the flanging process presents more challenges than metal spinning as forming takes place over a much smaller area and must typically achieve strict tolerances. These challenges include:
- Minimising material thinning – when the edge of a dished end is flanged, it can cause the metal to laminate. Efforts should be made to minimise lamination as it can lead to increased material costs. However, this can be difficult due to the large forces being exerted on the metal, especially when dealing with less tough materials.
- Regulating pressure – flanging machines must be configured properly to make sure the rollers are in constant contact with the metal and that the correct pressure is being applied. This will help guarantee the process can be completed in as few passes as possible.
- Achieving precise tolerance – flanged dished ends typically come with very small tolerances, sometimes as little as +/- 0.5% of the part diameter. This is necessary because dished ends must be able to fit flush within the larger part they are intended for, as this allows for effective welding.
- Surface imperfections – even small bumps and chips in the surface of the metal can result in waste as some parts fall outside of the necessary tolerance. As such, it’s recommended that material stock undergoes additional quality control checks after initial spinning.
Looking for an expert dished ends manufacturer?
Companies looking for metal spinner near me in the North East, whether it’s for dished ends, pressure vessels, tank heads, or bespoke projects, can make use of Tanfield Metal Spinners. Our factory space, coupled with a large range of tooling and machinery, gives us the capability to complete flanging works and much more. We achieve a high level of precision in dished ends manufacturing through quality control and testing. Many of our customers supply us with a cylinder or jig so we can hit their specifications exactly. Simply get in touch to chat about which of our services will be best suited to your project needs.